
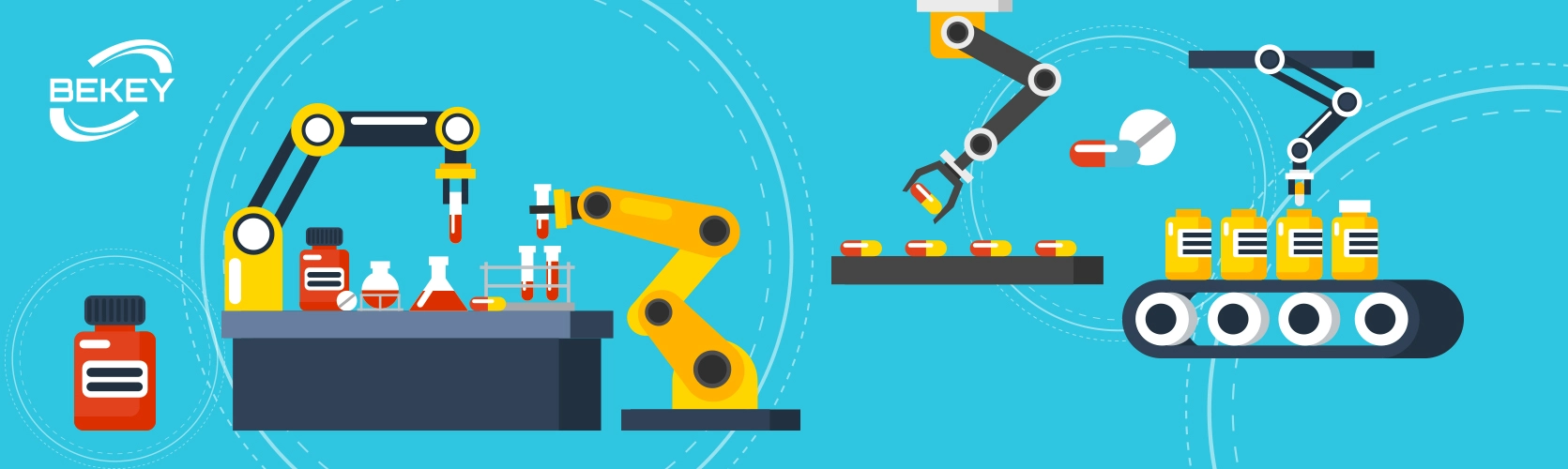
How automation in pharma optimizes cost and reduces errors
Complex systems possess a potential for catastrophic failure.
— Richard I. Cook, MD
Supply chains are complex systems, and the more individuals, interactions, and other components a system contains, the higher the probability that it will break down. Supply chains also largely depend on how well people who work in there can focus; do repetitive work; keep in mind large amounts of information; document everything; etc. That essentially raises the likelihood of failure. Of course, one failure is not enough to break down everything. But a lot of tiny errors, mistakes, overlooked details, — which are absolutely natural — and a manufacturer has to deal with a cascading failure. PR crisis. Bad supplies causing bad things. Low profits.
In the pharmaceutical industry, a precarious vibe of supply chain essence gets very expensive — and, potentially, life-threatening.
Expensive because of the high cost of drug development (and, of everything, actually, related to it). Because some drugs are very sensitive to environmental conditions. Because counterfeit drugs enter the supply chain so casually, as if they own it, — and it’s not just online stores, it’s also pharmacies and hospitals. You got the idea.
Plus, the pharma businesses need to move faster if they want to survive the competition — and they need to adapt all the trendy and hot things from out there, like security, precision medicine, and value-based care.
That’s precisely where automation comes (but only after analysis of “what is broken” and “what can be broken later.”) Let’s explore few cases of injecting automation into different processes in the pharma supply chain.
Automation in drug discovery and clinical trials
The volumes of drug development are growing, according to a number of approvals provided by FDA, — and the drug prices are highlighted as a point of controversy— to put subtly— especially in the USA.
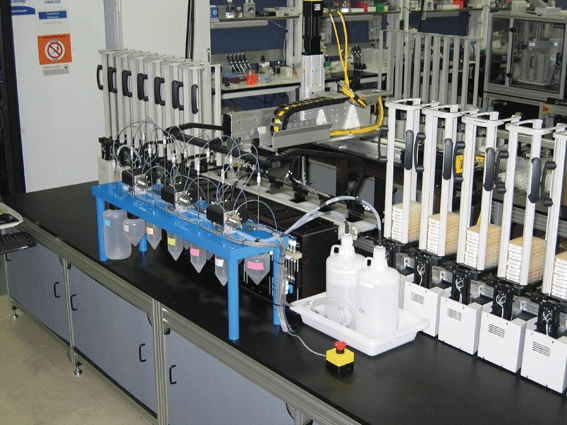
A laboratory is one of the most perspective places for automation: there is a way to unleash employees’ productivity and workflow efficiency both via software and devices automation. For instance, Scripps’ Lead Identification Division combines robotics, life sciences, and informatics to perform High-Throughput Screening — a process that tests thousands of drug-like compound to see if they’re biologically active, if there are enzymes or ion-channels, etc. Using technology, scientists understand what’s going on in compounds better — which ultimately allows them to understand how different diseases react to these ingredients and compare them.
Two years ago, Nature conducted a survey among researchers on reproducibility crisis. It occurred that 70% of researchers tried and failed to reproduce another scientist’s experiment. Among reasons that might have been leading to such results, journal lists “small things” like shaking or stirring a sample, and selective reporting. Better statistics and better mentorship were listed as the best “pills” to fix the reproducibility issues — and when we talking about statistics, it would be really good to mentioned automated algorithms that reduce errors and take into account all that human eye can miss.
Scotlands’ NHS Tayside case may serve as a classic example of automation in the labs. Siemens Healthcare Diagnostics provided a lab with a solution to reduce waste of resources. Lab staff was able to run cross-disciplinary tests faster and spend more time analysing insights from the results — without parsing a thousand tubes through these tests by themselves.
As for shaking hands and samples, it’s a good time to remember robotic arms.
By the way, clinical trials are also a fitting place for automation. One of the biggest challenges for research organizations is helping trial participants to make it through the funnel: to complete a randomized trial. Disengagement is a financial issue for pharma, and a simple app that allows participants to be on track with a trial progression — and allows their “managers” on CRO’s side to see if their mood isn’t in a good place through mood trackers — can help deal with that issue. Automated solutions can also process consent forms and trial results quickly, streamlining the process and giving researchers means to plan their next steps.
Automation in drug development
In August 2019, pharmaceutical company Nephron partnered with Clemson University to develop a robotic solution for syringe-filling. Nephron’s CEO, Lou Kennedy, said that syringe automation will help the company ensure the manufacturing stays safe and efficient.
Veli Matti Pihalja from Fermion described another case of automation adoption: a system that eliminates human errors through electronic recipes and batch records. The bar code system Fermion use in API (active pharmaceutical ingredients) drug manufacturing automatically weighs ingredients that will go into batches. Earlier, the company needed two employees to double-check everything’s correct in the process. Needless to say, such an approach cuts development costs largely due to speed, precision, reduced the amount of discharged patches and save employees’ time.
Lonza’s Xcelodose Precision Powder Micro-Dosing System which was often used in AIC studies (“API-in-capsule” — when an active ingredient or a blend are dispensed into a capsule in the process of manufacturing) fights the issue of environmental sensitivity — no human involvement anywhere near the drug is needed.
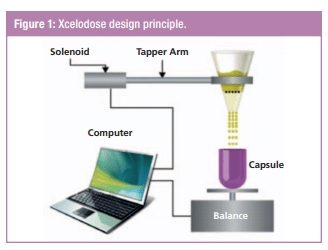
The amount of powder that is designed to go into a capsule is defined via computer — the parameters can be adjusted accordingly to characteristics of a material and dosage. The system controls the filling process in the real-time mode and, after completion, it can recognize and remove units that don’t fit into a projected weigh. So, again, — less human error, more precision. Another case of addressing drugs environmental sensitivity is AST’s robotic filling solutions. They are designed to process vials, syringes, and cartridges in “no-touch” mode — and they include barrier systems and aseptic isolators to protect contents of vials. Plus, these systems can recognize if a vial misses a stopper — and add it in the vial in the second “round” of drug processing.
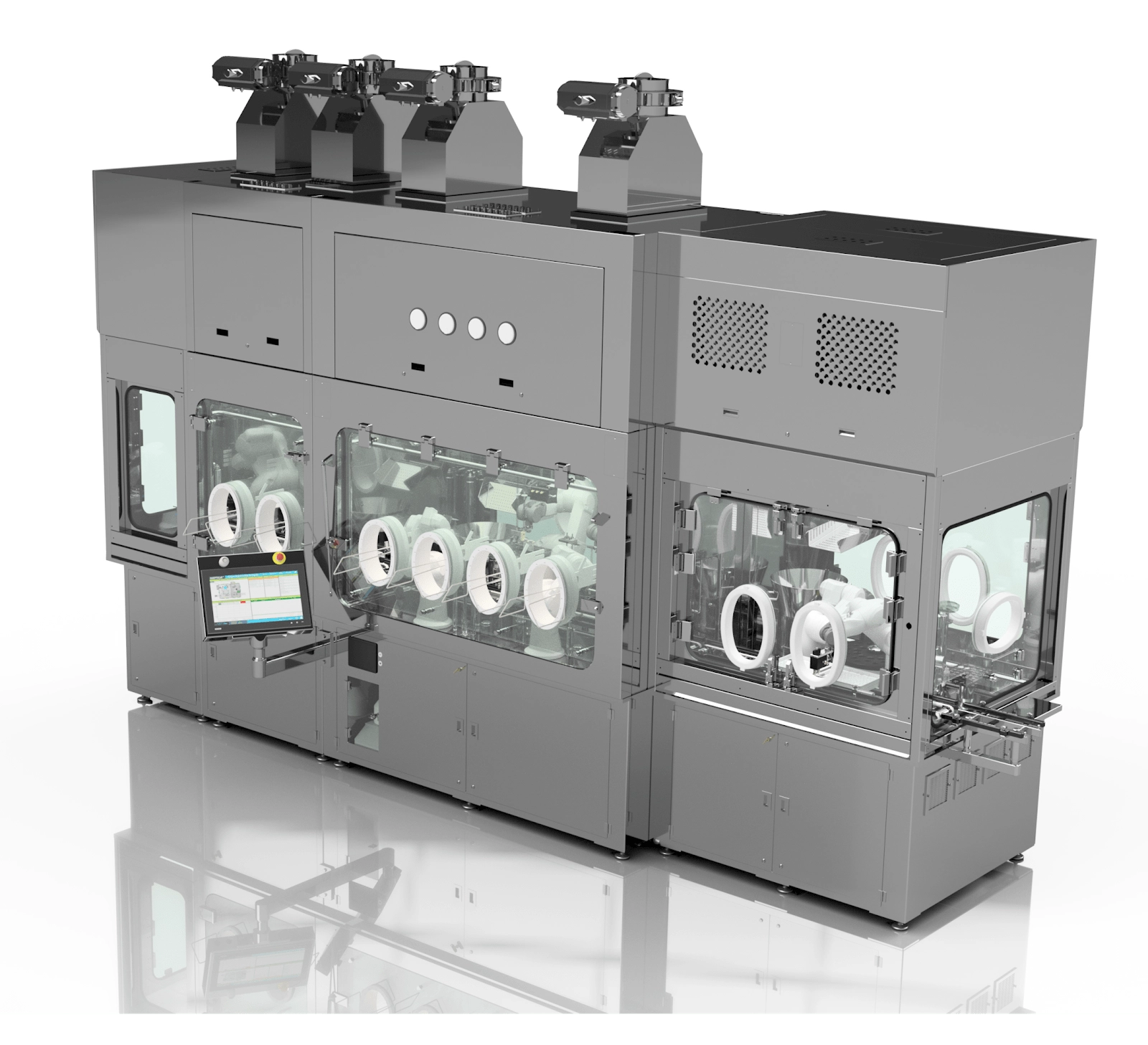
Recipe-driven software platforms allow drug manufacturers to put in the system a recipe with needed information about the drug dosage, press “Enter,” and go for a coffee. Returning, they’ll see closed vials and documentation for them.
It’s not a very scalable solution yet, and it doesn’t fit into workflows of pharmaceutical companies that produce large amounts of generics, — but the time of precision medicine and personalized medication programs truly comes, and that is where such systems will be of use.
As you can see, robotic solutions give pharma means to reduce human errors, accelerate drug development, enhance quality control and, therefore, content uniformity. Plus, most of the robots are designed in an ergonomic and easy-to-install way, so they’re pretty comfortable to adopt by drug manufacturers.
Automation in pharma supply chain logistics
Tom Peters, co-author of In Search of Excellence— a book on business management,— once argued that when leaders win, they do it not through strategy or vision, but through logistics. Quality, timing, and exemplary service delivered in hand of a person-in-need is made possible by superior logistics. Good logistics means employees feel in control of the production and distribution; it means nothing would be lost, expired, or damaged— and, if some of these things happen, logistics provides appropriate damage control.
Organizing lean, clear, and secure logistics for pharmaceutical supply chain starts from packaging and warehouse management.
Packaging should consider both the stability of containment and damage protection— from environmental factors as well. The automated system for packaging, therefore, must include algorithms to place a bottle in the right way, label and cap it. At the same time, it should contain the means to monitor the whole package for fallen bottles and other inconveniences.
Now, we’ve already talked about bar codes for weight checks— in the packaging case, though, they are becoming tools for monitoring where a package is; data nature and amount of drugs in a pack are gathered by machine vision. Packaging lines and robots that operate over them must be integrated with software that is similar to business process automation solution — the Enterprise Resource Planning (ERP) system. ERP reflects the whole process of packaging and preparation for shipment, automatically conducts documentation and notifies employees, if something went wrong.
Automated logistics solutions help companies speed up the material flow, build an uninterrupted chain, and establish quality control. With them, pharma companies and distributors build traceable, transparent process of drug delivery, monitor expiry dates, and, in general, have more control over where the product goes and how it, after getting to an end-customer, performs on a certain market (if there is an integration with the frontline, of course.)
Sensors that detect unauthorized unpacking and notify manufacturers about that help manufacturers to address fraud. Same sensors — temperature- and light-sensitive, as you’ve figured — if combined with a bit of Internet of Things — inform manufacturers, if transportation conditions become inappropriate for a certain drug.
Final thoughts: Prepping for the future
All these nice solutions may seem mundane, however long we talk about patient safety and all these soft and nice things — at least for stakeholders — but consider this: this spring, Amazon has acquired PillPack. That’s an online pharmacy with an 800+ people workforce with extremely low margins that managed to start shipping drugs to every state except Hawaii and developed an automated refill management system. They are very customer-oriented. It’s predicted that soon Amazon will introduce a model that will optimize logistics cost and make distribution quicker and stable. In that case, other pharmacies and drug manufacturers will have to keep up with a newly introduced norm: an online-pharmacy is significantly closer to an end-customer and able to deliver more personalized, targeted services.
Customers expect to receive affordable, accessible, and efficient medicine — and drug manufacturers, sooner or later, have to think about how to cut costs and improve their delivery process. Warehouses will change, adapting for on-demand drug development; manufacturing will become distributed, personalized, smaller.
There are a lot of solutions that don’t include automation—or relate to it indirectly. Artificial intelligence, combined with automation, can, as it occurs, largely boost drug discovery: automation algorithms processes tons of data and AI’s figuring out patterns in the scope. Blockchain can secure drug distribution— the technology looks especially promising, paired with Internet-of-Things sensors and patches we’ve talked about. All of these technologies — combined or separated — will be there when the time of DNA-based treatments and pill-for-demand comes.
This article is a part of our healthcare software development tech series. Check out instalments on how automation enhances EHR and how digital transformation can change emergency services.
Tell us about your project
Fill out the form or contact us
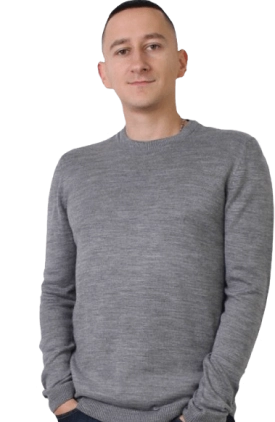
Tell us about your project
Thank you
Your submission is received and we will contact you soon
Follow us